
Design Guide 2 - Effects of Stripe Width & Optimum Magnetic Head Performance
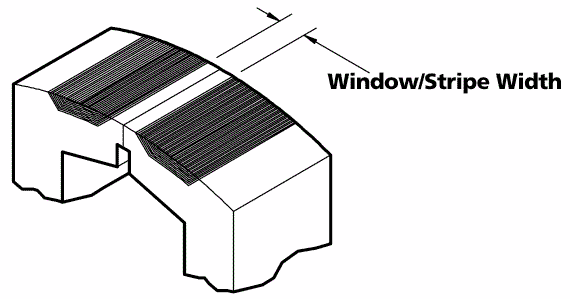
New soft core head profile
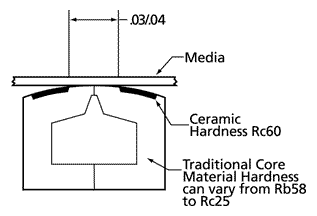
Condition of a new ceramic coated traditional material magnetic head. The magnetic head contour is shaped in a manner to insure good head gap to media contact. The traditional core material containing the head gap is in a plane slightly elevated above the ceramic. Magnetic heads in this condition will generally perform flawlessly.
Process of wear on soft heads
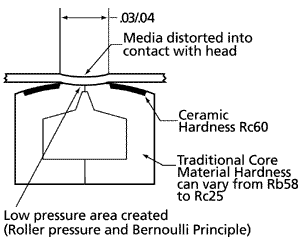
Condition of a ceramic coated traditional material magnetic head. The softer traditional material magnetic core, sandwiched between the two adjacent areas of ceramic, had worn down flush with the ceramic. As abrasive magnetic media continued to pass over the head it wore in a concave manner (scalloping). This condition is caused by a low pressure area created at the top of the head and roller pressure on tickets. At this point the low pressure area is still able to maintain magnetic head gap to media contact. The magnetic head continues to function.
Spacing loss due to scalloping and dirt accumulation
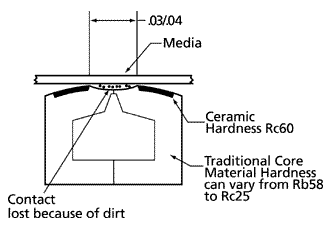
Condition of a ceramic coated traditional material magnetic head showing effects of scalloping to a point that low pressure (Bernoulli principle) can no longer maintain magnetic head gap to media contact. The magnetic head fails dramatically, no longer capable of reading or writing. In this case the head fails and is worn out. (see Spacing Loss figure below).
Traditional solution
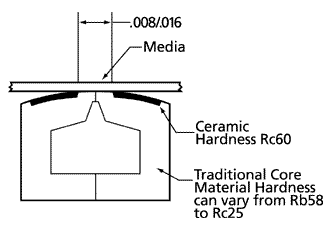
Condition of a ceramic coated traditional material magnetic head showing what the industry has considered a solution for the scalloping problem. The stripe width has been decreased from .030/.040 to .008/.016. The reduced distance between the two ceramic areas lessens the amount of scalloping and extends operating life. This solution has some definite disadvantages. The exposed magnetic material on either side of the head gap is only .004 to .008 wide. This is not enough magnetic material to be able to efficiently record or overwrite high coercivity media. This is not a viable solution for high coercivity write heads. In addition this limits head manufacturers to using old technology stamped core laminations versus the modern practice of using photo-etched laminations in a frame.
Supermium® solution
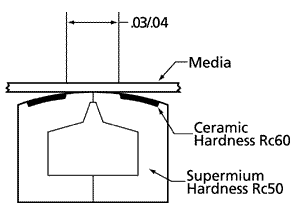
Condition of a ceramic coated Supermium® core magnetic head, showing wear characteristics exhibited throughout the life of the head. The Supermium® core material is almost as hard as the ceramic. Rc 50 for Supermium® and Rc 60 for Ceramic. Scalloping does not become a factor. In addition the hard Supermium® core material retains its original surface finish much longer than the softer traditional core material, significantly extending card or ticket life. When laminated this material has adequate magnetic properties to be used for encoding high coercivity media, currently up to 2750(oersted).
Spacing Loss
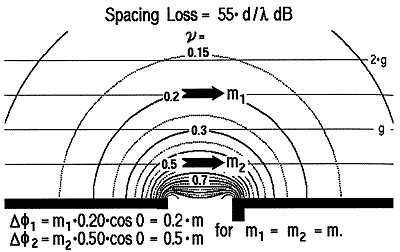
Spacing loss reduces the flux contribution from magnetization spaced away from the head surface.
The Complete Handbook of Magnetic Recording 4th Edition By Finn Jorgensen McGraw Hill 1995.
Magnetic Core Materials
Mumetal
- ASTM A-753-78 Alloy
- Fe Ni
- Hardness Rb 58
Hypermium™ I
- ASTM A-801 Alloy Type 1
- Fe Co V
- Hardness Rc 25
- Annealed to brush proprietary specifications
Hypermium™ II
- ASTM A-596 Alloy
- Fe Ni Mn
- Hardness Rb 62
- Annealed to brush proprietary specifications
Supermium®
- Al Fe Si
- Hardness Rc 50
- Processed for enhanced magnetic characteristics, increased hardness and reduced grain size
Supermium® 2.75
- Al Fe Si
- Hardness Rc 50
- Material specially processed to produce core laminations for high coercivity, 2750 Oersted media and high frequency applications
Supermium® 3.5
- Al Fe Si
- Hardness Rc 50
- Processed to produce core laminations. A proprietary magnetic head fabrication process produces a magnetic head capable of encoding high coercivity media up to 3500 Oersted
CC (Ceramic Coat)
- Hardness Rc 60
- Plasma sprayed coating of AlO2 and TiO2 producing a hard wear surface
Plasma sprayed coating of AlO2 and TiO2 producing a hard wear surface
On ceramic coated magnetic heads the width of area of magnetic cores presented to the media is determined by the window width at ceramic coating. The optimum width dimension is dependent upon the mechanical hardness of the magnetic core material.
Soft core materials such as Hy-Mu 80 with window width > .020 inches exhibit short operating life due to head scalloping causing spacing loss failure. The solution has been to narrow the stripe width to a recommended .008 to .016 inches. However it must be recognized the narrow window limits the magnetic head to use with low coercivity media and a narrow window width tends to increase manufacturing costs.
One hard core material, Supermium®, which has a material hardness approaching Ceramic is not subject to scalloping. A larger more cost effective window width can therefore be used. The recommended window width for Supermium® .030 to .040 inches. At the wider width Supermium® does not suffer scalloping and allows high coercivity (2750 oer) performance.
By Larry W. Ditty
Executive V. P. Technology
brush Industries, Inc.